Artisan Tile Installations for Public Spaces
The tiles are made by fusing a thin veneer of glass onto a ceramic tile surface. Each tile pattern is individually designed and handmade. A broad palette of colors are attainable and I’ll try to match your carpet samples.
There is no AI, 3D printing or digital manipulation involved in the process.
The 6″x6″ individual tiles and groups of 25 tiles (30″x30″) boards are presented as color/pattern studies. Process lends itself to scale-up production for interior wall spaces with large format installations:
- Airports • Libraries
- Hotels • Government buildings
- Education institutions • Convention centers
- Office building lobbies • Hospitality buildings
- Casinos • Civic/cultural spaces
- Transportation terminals • Residential interiors
- Healthcare waiting areas • Music venues
- Courthouses • Places of Worship
Installation of the tiles use standard ceramic tile mounting methods. They are UV and water resistant, durable and require minimal maintenance for upkeep.
Process: Though, this project is about making art, I bring a designer’s perspective in seeking collaboration with those involved for a successful outcome. My career as an industrial design consultant involves working with the client; architects/interior designers, facilities owner, installers and the end-user, the viewer who will benefit from this effort. Projects start with a design brief outlining the scope of the project, costs and deliverables. I will provide a series of sketches, color studies on tiles, a guide map for installation, and sample boards for all to sign off on before the final design is fabricated.
Material: Glass is unique in that it has phase change properties, where it can be altered from a liquid to a solid and repeatedly back again. During these alternative physical transition periods, I’ve developed a process to adjust and control the dimensional placement of color across the tile surface. The visual effects happen when you apply high temperatures to the uniquely processed raw materials. Combined with research in inorganic chemistry, fractal geometry and a smidgen of magic, the process creates a pareidolia effect to offer the beholder an ability to envision visual patterns, imagine objects or create stories out of randomness.
Production: I use off-the-shelf materials traditionally used in the manufacturing of ceramic tile glazes; frits, clays and colorants. I utilize ready-made bisque tiles that have industry standard grooves on the back and lugs on the sides for proper installation. All materials are readily available from multiple suppliers, which creates a robust supply chain. I’ve invented, produced and use proprietary tile setters (kiln furniture) specifically for 6” tiles to support the tiles during the kiln firing process. Employing them I can fire 34 sqft. vs. 16 sqft. (Skutt 1227) per kiln load. An increase of 112% in production, with a 56% decrease in energy usage/costs per firing.
I use 100% renewable resources to fire my kilns.
Dazed & Glazed, LLC is a small business. The tiles are locally designed and handmade in the US.
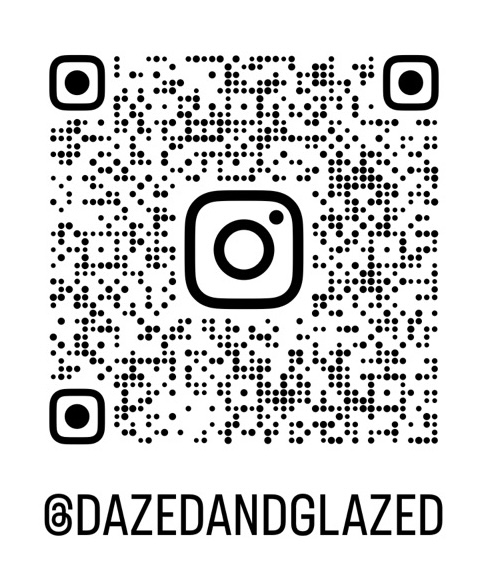